CNC (computer numerical control) is the automation of machine instruments through the use of computers which have been programmed to execute any number of commands. From wood routing to laser cutting and 3D printing, there are CNC machines for nearly every commercially utilized manufacturing process and application. Precision CNC machining works with a variety of materials including metals, woods, acrylics, foams, and thermoplastics.
CNC systems vary in their composition as some systems combine all necessary tools into a single unit while other designs may consist of individual, tool-specific units interconnected by external controllers. Regardless of their specific composition, all modern CNC systems provide automation of the design and manufacturing process of a machined part. While CAD (computer-aided design) software defines the physical boundaries of an end product, CAM (computer-aided manufacturing) software translates those dimensions into manufacturing commands. Through the use of post-processing software, these commands are translated and loaded into a CNC machine.
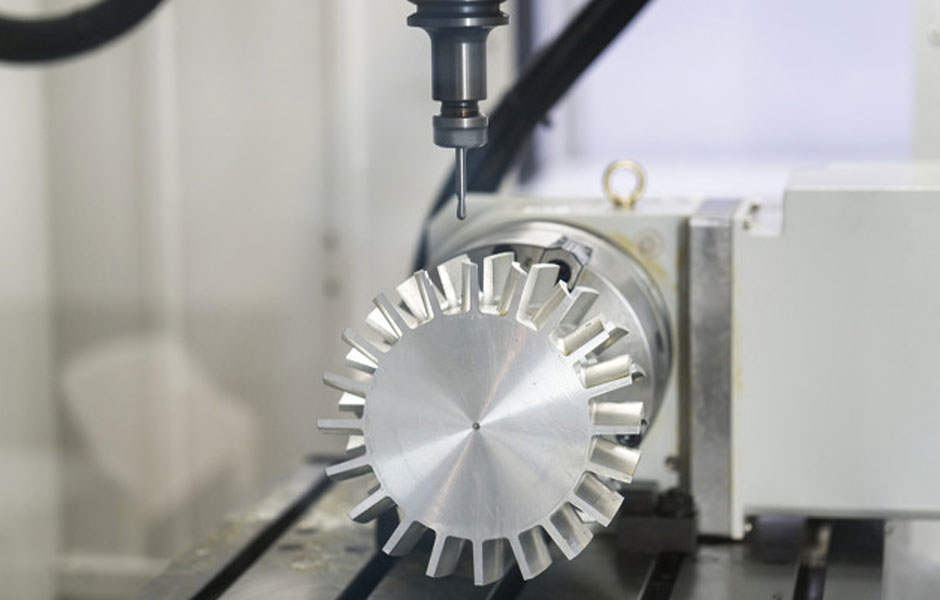
Following are some of the benefits that manufacturing organizations can accrue by employing precision CNC machining for parts manufacturing:
Fully Automated: CNC machines are fully automated, which means they help reduce dependence on human machinists. CNC machines don’t require regular monitoring, and can be left unattended while they complete the machining work. This allows manufacturers to employ fewer people, and use the existing workforce for more productive tasks.
Fewer Downtimes: Most CNC machines can be operated 24/7/365, which allows manufacturers to increase their productivity, and meet their deadlines easily. These machines are only shut down for a few hours for maintenance.
Consistent Product Quality: Human machinists can be prone to mistakes when creating components in bulk. CNC machines can produce exact replicas of machine parts every time they are used. This is very important in the industry, where a small defect can lead to component rejection and replacement, which can take excess time, effort, and expenditure.
Ideal for Producing Complex Parts: Multiaxis machining refers to the type of machining in which the machine can be made to move in multiple axes, while manufacturing machine parts out of large metal sheets. Many precision CNC turning manufacturers provide 3, 4, and 5 axis CNC machining. Multiaxis machining aids in the manufacturing of complex parts with curves or curved holes.
Flexibility: CNC machines provide great flexibility over regular machining techniques. The machine allows for reprogramming and software updates. This allows machinists to alternate from making one machine part to another quickly. Also, they can store the software programs for future reference or reuse.
Easy to Operate and Learn: The operation of the CNC machine is easy to understand. The virtual commands can make the learning experience easy for novice machine operators. Once the first part is inspected, the ongoing production batch requires no inspection at all. The machine can be used to make plastic and metal parts easily.
Applications of Precision Machining
Precision CNC MachinePrecision machining produces parts to a much more exacting standard than baseline CNC machining. It is an excellent solution to meet stringent project requirements, such as:
- Tight tolerances. With the right equipment available, precision machining can produce parts with tolerances as small as ±0.0001″.
- Repeatability. Successful precision machining means that parts must be able to be machined to the same tight tolerances repeatably from part to part.
- Volume. Precision machining practices can handle virtually any production volume requirement ranging from prototypes to high-volume production runs and blanket orders.
Computer Numerical Control (CNC) machining is allowing manufacturing engineers to transform machining from a conventional manufacturing process into a precise art. Manufacturers are keen to adopt CNC machining due to several benefits in terms of precision, time, costs of labor, and materials.